Six Sigma’s Define, Measure, Analyse, Improve, Control (DMAIC) methodology has been around since the 70’s but what is it actually used for? The text books and official answer will say “it’s a widely used and recognised tool to reduce variation” but it’s much more than that. Although it was born from improving manufacturing processes by the likes of GE, Motorola and Toyota, it’s now used worldwide across every industry. In my experience of using the methodology over the past 15 years, the DMAIC methodology can be used to resolve business problems of any kind. It’s a flexible tool that can be adapted to any situation with no boundaries on problem type. It’s this flexibility that I think contributes to its success.
The below graphic illustrates the journey a problem goes through as it goes through the DMAIC phases. It explains how defining the problem at the beginning and identifying all the possible causes can help you conclude with the best solution.
Fig 1.1 DMAIC’s problem solving journey
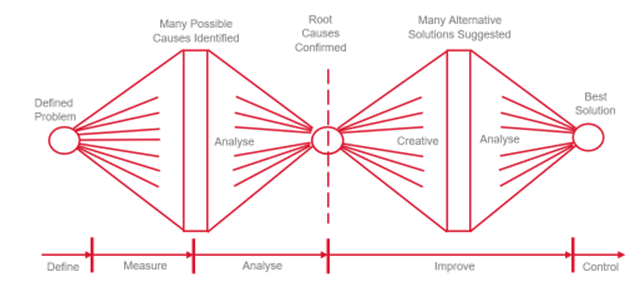
In this blog, I explain how the problem moves through the different phases of the DMAIC methodology.
Defining the problem
What sets Six Sigma’s DMAIC methodology apart from many other business tools is that it starts with the problem. There is no limitation to what the problem can be; it can be large or small, easy to fix or complex. Either way there is not a business out there that doesn’t have a problem that need fixing. Examples could be:
- We can’t respond to our customers quick enough
- We have errors, missing information or defects in our products or services
- We can’t produce enough of our products within the normal working day
- We have variation in our process and don’t know how to reduce it
- Our processes are very manual and inefficient
Having no problems is a problem!
Measuring the problem
How will we understand the extent of the problem and all the possible causes if we don’t document the process and measure it? By mapping the process, we can get down on paper what’s going on, who’s doing what, what systems and files are being used, where rework loops exist; it’s all there on a page. Then when you think you’re happy with the process, there’s measurement. How long does it take to complete each activity and what’s the delay between each activity? It’s only by collecting these two measures that we can add them together to understand the total cycle time. Measurement helps us baseline the process performance and say how the process is performing at this point in time. We are now in a position to see the many potential causes to our problem.
Analyse the problem
How do we take the many possible causes to the problem identified in the Measure phase and bring them down to the vital few that will have the biggest impact in resolving the problem? That’s what the Analyse phase of the DMAIC methodology sets out to accomplish. Through analysing the process cycle time and the data around the process, root causes start to emerge. These potential root causes are often best captured from those performing the process. Using various tools such as 5 Why’s and working with the team, we can identify the root causes to the problem taking the many potential causes and reducing them to the vital few.
Improve the problem with the right solution
Now we understand the root causes to the problem, we need solutions. Working with the team responsible for undertaking the activities, we would brainstorm solutions. This is the time to get their thinking hats on. What are all the possible things that can help resolve the root causes to the problem? At this point, you should have a white board full of potential options. However not all of all of the potential solutions will be feasible or deliverable, particularly if you’ve done some ‘Blue Sky Thinking’. Some solutions will provide greater benefits for less effort than others and some will meet your solution requirements more than others. This is where tools such and the Pugh Matrix, Solution Matrix and Effort vs Benefits analysis come in. These and other Six Sigma tools will help you bring all those potential solutions down to the best one. Well, it’s time to deliver the project and implement the best solution now.
Controlling the changes
So the problem has been understood and documented, we have mapped out the problematic process and measured it, we have analysed the data around the process to identify root causes and come up with the best solution to resolve the problem. What’s next? We’re done, right? How do we know that the solution you put in place has resolved the problem? By continuing to measure the new process, we can understand it’s new performance and confirm that it’s performing in a way that we expected it to. We can ensure the new process is in control and stable. By comparing the measurements gathered in the measure phase, we can spot the improvement in process performance, demonstrating the benefits of the solution. Continued measurement will enable you to see if the process can be changed again for further improvement or investigate why the process performance has deteriorated.
Conclusion
Six Sigma’s DMAIC methodology is a data-driven problem solving tool. For this reason, it’s unique. Six Sigma’s Define, Measure, Analyse, Improve, Control phases are the framework to help you gather the required data, analyse it and then achieve that best solution. The types of problems that it can help you resolve are limitless. The industry types it’s been used in have also been limitless.
For a discussion about how your processes can be improved, get in contact with us. We’d be happy to share our wealth of experience, knowledge and expertise.